We Provide Commitment
Our products meets critical requirements of reliability & safety in nuclear industry. Our experience in handling affects on seal performance and life are within regulatory and technical parameters.
Stein products are especially effective in meeting the critical requirements for reliability and safety needed in the nuclear industry. Our extensive experience with issues such as the effects of radiation, decontamination and vibration or misalignment on seal performance and life ensures that seals operate well within regulatory and technical parameters.



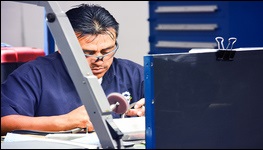

Nuclear Seals and Sealing Systems
Stein Seal Company has been a major player in the Nuclear Mechanical Seal industry dating all the way back to the 1980’s. From designing the first commercial hydrostatic reactor coolant pump (RCP) seal for the pressurized water reactor (PWR) market, to designing hydroload circumferential pump seals for the Superphénix fast breeder reactor (FBR) in Switzerland, and even designing pump face seals for the Westinghouse liquid metal FBR; Stein seal has been a leading innovator since their first inception into the market.
Stein Seal Company specializes in developing shaft seals for Reactor Coolant Pumps (RCP). These seals are found within RCPs in nuclear power plants across the U.S. and Europe. In a nuclear power plant, the RCP a piece of machinery that stands is responsible for maintaining optimal temperatures by pumping large volumes of coolant through the reactor core in order to dissipate heat generated from the fission reaction. If an RCP were to fail in a nuclear power plant, the plant would require immediate shut down; this makes it vitally important to have a reliable sealing solution on the main shaft of one of these pumps.
Stein Seal Co. has developed a three stage sealing system for the RCP main shaft consisting of a number one, two, and three seal. The number one seal is the first line of defense against the high-pressure water flowing into the RCP at 2,250psi. The number one seal is a film riding seal that operates on converging surface tapers that are engineered to provide a controlled leakage through the seal. The number one seal provides over a 98% reduction in pressure within the RCP, reducing the pressure from 2,250 psi down to 30 psi. The remaining two seals are contacting seals that consist of a sealing component and its corresponding runner. These two seals further reduce the pressure from 30 psi down to atmospheric pressure before leaving the RCP. It is important to note that although a large majority of the pressure reduction is achieved in the first stage of the sealing solution; all three seals are capable of independently maintaining proper plant operation for safety purposes.
Due to the extremely critical applications of their seals, stein seal must ensure proper fit and function prior to installation at any of the dozens of nuclear power plants that they supply. This is accomplished through their state of the art testing laboratory. With various testing rigs available all able to withstand pressures exceeding 2200psi, Stein Seal can perfectly mimic the applications of their seals and analyze the real world performance, all in house. This allows Stein Seal to fine-tune their seals to ensure that they meet all of the performance expectations of their customers, before every shipping the parts.