WE MAKE FLYING SAFE
Our seals will withstand the wide range of conditions that will occur during normal operations including temperature extremes, high speeds and strong vibration.
Stein has developed an in-depth understanding of the extreme operating conditions to which seals used in the main shaft bearing sumps, gearboxes and generators in aircraft engines are subjected. Each precision sealing system is custom designed to perform flawlessly with low wear and long life. Our seals will withstand the wide range of conditions that will occur during normal operations including temperature extremes, high speeds and strong vibration.
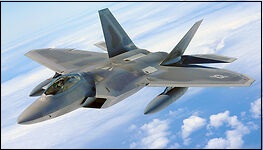



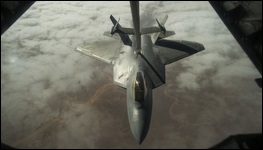

Aerospace Seals and Sealing Systems
There are few applications that are as challenging to the seal designer and manufacturer as Aerospace seals. Main shaft seals used for aircraft must function flawlessly while operating in an environment under extreme temperature, pressure and speed variations, low weight requirements, long wear life and minimal leakage. Auxiliary seals used to seal gear boxes, APUs and electrical generators also present engineering challenges with potentially reversing pressures, weight limitations and high speed.
Stein Seal Company is the leader in this field with many years of experience in seal design and manufacture for the leading turbine engine manufacturers world-wide. Since our founding in 1955, we have helped develop seals for many of the newest commercial engines as well as those used in both military and business jet engines. As we strive to develop the best possible seal system for these applications, we have developed design and manufacturing programs that help us do this work better.
When possible, we try to work with the engine designers in the early stages of the engine design process to help design the seal environment for the best possible performance of the seal system. Often the amount of space allocated for the seal, or the position of the oil nozzles or oil drains will affect the performance of the seal. Typically, we prefer to make the mating seal component, since the sleeve or mating ring geometry is critical for proper seal performance.
We offer a range of sealing solutions including circumferential seals, face seals, bushings, and brush seals. Our circumferential seals can be pressure balanced for longer life and higher pressures when necessary. Our hydrodynamic face seals are designed for minimal wear and long life. Designs for gear box seals allow for minimal load on the seal face.
In the Aerospace seal market, documentation and traceability are critical for maintaining product quality. Stein Seal’s quality system has been certified by Performance Review Institute as meeting AS9100D as well as ISO 9001:15. We perform 100% inspection on our Aerospace products and have a fully trained Designated Supplier Quality Representative team for over inspection. We also maintain NADCAP certification for several special process applications.
Machining of Aerospace seals can be challenging, since many of the products are made of exotic material and all parts are thin walled to reduce weight. Flat surfaces with fine finishes are critical for the proper functioning of seals. Stein Seal maintains a high precision machining operation that includes CNC cylindrical grinding, 5 axis machining, numerous machining cells and unmanned 24-hour mill-turn centers. This allows us to offer high precision machined parts at reasonable prices.
While we bring a tremendous amount of experience to the design table, dynamic testing of the proposed seal assembly is sometimes necessary to verify a design prior to operation. We maintain a fully staffed dynamic test department that is skilled in dynamic test simulation and can test the final seal product under normal or non-normal conditions. We have over 20 dynamic test set-ups and can reproduce most engine conditions.
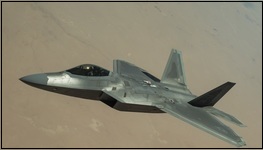
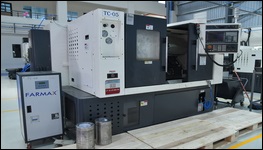
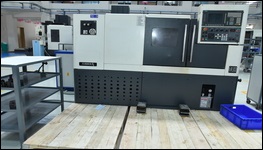
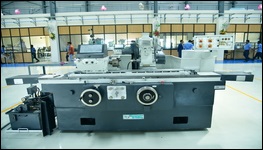
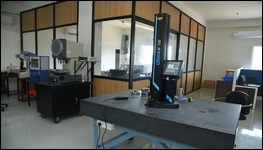
Aerospace Seal Repair Centers
We believe that when we sell a seal, we are responsible for the overhaul of that seal for the life of the engine. With most of our seals, the carbon, which typically exhibits the wear, can be replaced at a cost significantly lower than the price of a new seal assembly. The replacement of the carbon results in seal assembly with the same additional life as a new seal.
Stein Seal Company has established two repair centers for the rapid repair and overhaul of aircraft mechanical seals and related components. Our initial repair center, located in Pennsylvania, was established many years ago and is certified by both the FAA and EASA as a repair center. More recently, we have started a second repair center, also certified by EASA and the FAA, in the Czech Republic to service customers located in the European Union and elsewhere. Our Czech facility employees are multi-lingual, which helps in communicating with the diverse population they serve.
Generally, we are overhauling mechanical seals that we originally designed and manufactured for the engine manufacturer, so we have an appreciation of the detailed requirements needed for the seal to function correctly. Some of these OEM customers have agreements with Stein Seal for us to provide overhaul services for the seals. Our understanding of seal design and manufacture is necessary for the successful overhaul of seals not manufactured by us as well.
The typical overhauled product includes main shaft bearing sump seals that could be either face or circumferential seals. We also overhaul gearbox type face seals with varying geometries. Our employees are skilled in precision lapping for critical surfaces, and we have “Super-finish and grind capabilities for the repair of sleeves and mating rings.
Both of our repair centers are well equipped with access to CNC mills, lathes, and grinders. In addition, we have static test set-ups that can measure seal leakages down to very low levels, and if necessary, can dynamically test critical products in our dynamic test lab.
While most of our overhaul work is on applications involving commercial and business aircraft, Stein Seal has a long history of involvement on military aircraft and supports a variety of military programs. We welcome participation with various military arsenals in support of overhauling their seals and related components.